姜上泉老師簡(jiǎn)介
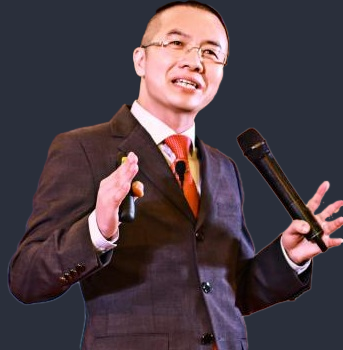
博客訪(fǎng)問(wèn):305289
姜上泉,中國降本增效咨詢(xún)領(lǐng)導者,著(zhù)名精益運營(yíng)專(zhuān)家,多家中國企業(yè)500強與全球企業(yè)500強降本增效和精益運營(yíng)顧問(wèn);曾受邀為北京大學(xué)、清華大學(xué)、中山大學(xué)、山東大學(xué)、上海交通大學(xué)等多所著(zhù)名大學(xué)授課;對豐田、本田、三井、海爾、沃爾沃、青島啤酒、中國中車(chē)、中國石化、中國兵器、中煙工業(yè)、國家電網(wǎng)等100..
姜上泉最新博文
- 戰略成本管理驅動(dòng)—降本增效中國行..
- 姜老師老師:開(kāi)源增收是最好的降本..
- 姜上泉老師:贏(yíng)在規劃和控制—降本..
- 姜上泉老師:溫氏股份佳潤食品精益..
- 姜上泉老師:太古可口可樂(lè )第2期降..
- 姜上泉老師:降本必增效,增效必降..
- 姜上泉老師:赤字接單,黑字出貨,..
- 姜上泉老師降本增效咨詢(xún)培訓:聯(lián)冠..
- 姜上泉老師降本增效咨詢(xún)培訓:20..
- 姜上泉老師:華潤三九降本增效行動(dòng)..
姜上泉主講課程
導讀:一家中國民營(yíng)企業(yè)500強,6年時(shí)間通過(guò)小創(chuàng )新小改善降低成本近4億元。6年時(shí)間,他們實(shí)施了23149項創(chuàng )新改善,創(chuàng )造了38747萬(wàn)元的降本成果,這是聚沙成塔,集腋成裘的經(jīng)典見(jiàn)證。 我們習慣于通過(guò)四級創(chuàng )新改善來(lái)推動(dòng)企業(yè)的降本增效。什么是四級創(chuàng )新改善?高層通過(guò)系統創(chuàng )新改善來(lái)推動(dòng)公司級降本增效項目,中層通過(guò)專(zhuān)業(yè)創(chuàng )新改善來(lái)推動(dòng)部門(mén)級降本增效項目,基層通過(guò)自主創(chuàng )新改善來(lái)推動(dòng)班組級降本增效項目,全員通過(guò)快贏(yíng)創(chuàng )新改善來(lái)推動(dòng)瓶頸級降本增效項目。 所謂的系統創(chuàng )新改善,就是瞄準公司級的大課題,組建跨部門(mén)團隊攻堅克難,即華為所說(shuō)的端到端的改善,但這種端到端的改善要有好的前提條件,如企業(yè)最高決策層的充分支持,中高層經(jīng)管人員的統一思想,各個(gè)部門(mén)之間良好的協(xié)作文化,激勵機制下的高效執行力。如果缺少這些前提條件,端到端的系統創(chuàng )新改善是很容易失敗的。 因此,大企業(yè)剛開(kāi)始導入降本增效項目或精益管理項目,我們建議先易后難,先小后大,先短后長(cháng)的循序漸進(jìn)式推進(jìn),當這種小創(chuàng )新小改善有效消除了小浪費和小損耗,星星之火形成了燎原之勢時(shí),大創(chuàng )新大改善自然而然就呼之欲出了。 今天,我們分享一家中國民營(yíng)企業(yè)500強的案例,看看這家集團如何通過(guò)小創(chuàng )新小改善達到大降本大創(chuàng )值的。 案例背景 某企業(yè)是中國機械工業(yè)重點(diǎn)骨干企業(yè)之一,總資產(chǎn)超過(guò)100億元,擁有農業(yè)裝備、環(huán)衛裝備、汽車(chē)制造、現代農業(yè)等產(chǎn)業(yè)。 然而,深耕農業(yè)裝備、環(huán)衛裝備、汽車(chē)制造等產(chǎn)業(yè),需要巨大的研發(fā)投入,雖然公司的優(yōu)質(zhì)產(chǎn)品頻頻出現在央視的報道中,但公司的凈利潤率卻始終沒(méi)有突破提升。 2010年,我到這家機械制造企業(yè)講了一場(chǎng)降本增效400多人的大課;2011年,這家企業(yè)全面啟動(dòng)了精益管理、降本增效的系列創(chuàng )新改善。 創(chuàng )新改善是只有開(kāi)始沒(méi)有結束的旅程。 時(shí)至今日,這家機械制造企業(yè)的創(chuàng )新改善已經(jīng)成為公司文化中最重要的DNA。記得2011年到2016年的6年時(shí)間里,這家機械制造企業(yè)實(shí)施了23149項創(chuàng )新改善,降低成本38747萬(wàn)元。 這家機械制造企業(yè)的創(chuàng )新改善是如何形成文化并創(chuàng )造良好財務(wù)效益的? 我整理出他們重點(diǎn)做的三件事: 一、掛牌成立勞模創(chuàng )新工作室,制定技師創(chuàng )新改善的執行制度和激勵制度,每年開(kāi)展產(chǎn)品創(chuàng )新、技術(shù)創(chuàng )新、管理創(chuàng )新項目的申報、立項、評選和發(fā)表,并每年開(kāi)展技術(shù)能手比武大賽。 二、公司頒布《持續改善程序》,規定創(chuàng )新改善的提報、評比、驗收流程,重點(diǎn)設置創(chuàng )新改善積分制度,創(chuàng )新改善的數量和質(zhì)量與員工的晉升、津貼、獎金掛鉤。 三、各個(gè)事業(yè)部的各個(gè)部門(mén),依據業(yè)務(wù)實(shí)際中存在的浪費和損耗制定《精益改善力》的訓練教材,明確“認識浪費、發(fā)現浪費、改善浪費”的方法、工具、流程,并對全員進(jìn)行訓練和通關(guān)考核。 案例剖析 改善一日易,維持百日難;改善固然可喜,維持更是可貴。 看完這家機械制造企業(yè)降本增效之創(chuàng )新改善的做法,好像覺(jué)得沒(méi)有什么特別的亮點(diǎn),仔細想想,他們優(yōu)先解決了創(chuàng )新改善中員工“不愿、不會(huì )、不能”中最重要的“不愿”,當“不愿”的問(wèn)題解決了,“不會(huì )、不能”的問(wèn)題就迎刃而解了。 降本增效的創(chuàng )新改善,被擠壓出來(lái)的員工干勁不會(huì )長(cháng)久,只有員工心底里認同的事情才能夠持之以恒。 當創(chuàng )新改善積分制度之創(chuàng )新改善的數量和質(zhì)量與員工的晉升、津貼、獎金掛鉤時(shí),員工們的創(chuàng )新改善意愿就由被動(dòng)創(chuàng )新改善發(fā)展到主動(dòng)創(chuàng )新改善,由主動(dòng)創(chuàng )新改善發(fā)展到主導創(chuàng )新改善。 降本增效之創(chuàng )新改善,先人后事,人在事前,先解決人的意愿問(wèn)題,就會(huì )起到事半功倍的效果。 這家機械制造企業(yè)的創(chuàng )新改善能做到十年如一日的堅持,并在堅持中不斷精進(jìn),還有一個(gè)至關(guān)重要的原因就是集團負責人的高度重視和親自參與,集團每年舉辦的各種創(chuàng )新改善活動(dòng),集團董事長(cháng)和總經(jīng)理都會(huì )親自參加。 降本增效導入的有效性=工具方法論×全員參與度×團隊領(lǐng)導力。毫無(wú)疑義,降本增效項目的成功,這家機械制造企業(yè)的團隊領(lǐng)導力是壓艙石。 6年時(shí)間,這家機械制造企業(yè)的創(chuàng )新改善能夠創(chuàng )造近4億元的財務(wù)效益,除解決了人的“不愿”以外,還有效解決了人的“不能”。 記得2011年到2016年的6年時(shí)間里,集團組織各業(yè)務(wù)部門(mén)編寫(xiě)了10多門(mén)《精益改善力》的訓戰教材,開(kāi)辦了10多期《精益改善力》的系列培訓,培訓結束后組織了10多次學(xué)以致用項目評審會(huì )和成果發(fā)表會(huì )。 在編寫(xiě)《精益改善力》系列教材時(shí),集團明確要求教材內容必須來(lái)源于本公司業(yè)務(wù),用于本公司業(yè)務(wù),指導本公司業(yè)務(wù);不得抄襲,嚴禁復制。 在培訓《精益改善力》系列課程時(shí),集團明確要求知識要轉化為行為,行為要轉化為績(jì)效;培訓完成才是開(kāi)始,成果達標才是結束。 無(wú)論是降本增效項目還是精益管理項目的推行,員工不愿做用激勵,員工不會(huì )做用培訓。這家機械制造企業(yè)降本增效的成功之處就是解決了人的“不愿”和“不能”;比創(chuàng )造近4億元財務(wù)效益更為可貴的是通過(guò)降本增效之創(chuàng )新改善,在實(shí)踐中培養了人才,激發(fā)了士氣。
降本增效短期靠工具,中期靠人才,長(cháng)期靠激勵。 案例啟發(fā) 三大創(chuàng )新改善齊頭并進(jìn) 這家機械制造企業(yè)每年開(kāi)展產(chǎn)品創(chuàng )新、技術(shù)創(chuàng )新、管理創(chuàng )新項目的申報、立項、評選和發(fā)表,通過(guò)技術(shù)創(chuàng )新?lián)屨冀?jīng)營(yíng)高度,通過(guò)管理創(chuàng )新保持經(jīng)營(yíng)高度。 很多企業(yè)在降本增效過(guò)程中推進(jìn)創(chuàng )新改善,多數是現場(chǎng)創(chuàng )新改善和管理創(chuàng )新改善,而真正涉及到產(chǎn)品成本的產(chǎn)品創(chuàng )新改善和技術(shù)創(chuàng )新改善卻廖廖無(wú)幾。 這家機械制造企業(yè)剛開(kāi)始主要由生產(chǎn)現場(chǎng)的操作員工和基層管理人員做一些六大損失和七大浪費的快贏(yíng)改善,后來(lái),逐漸發(fā)展到以技術(shù)人員為生力軍的創(chuàng )新改善。 雖然一家企業(yè)技術(shù)員工人數只占5%-10%,而正是這僅占5%-10%的創(chuàng )新型技術(shù)人才推動(dòng)了企業(yè)的可持續增效和降本。 三級經(jīng)管人員共同參與 小創(chuàng )新小改善用卡,中創(chuàng )新中改善用表,大創(chuàng )新大改善用書(shū)。“卡”即創(chuàng )新改善紙卡,重點(diǎn)是填寫(xiě)簡(jiǎn)單操作方便;“表”是創(chuàng )新改善項目表,重點(diǎn)是要能用一頁(yè)紙管控好整個(gè)項目;“書(shū)”是創(chuàng )新改善項目方案書(shū),重點(diǎn)是要能明確跨功能項目小組的責、權、利。 基層主導推動(dòng)小創(chuàng )新小改善(自主創(chuàng )新改善),中層主導推動(dòng)中創(chuàng )新中改善(專(zhuān)業(yè)創(chuàng )新改善),高層主導大創(chuàng )新大改善(系統創(chuàng )新改善)。 創(chuàng )新改善不是靠“1個(gè)不平凡的人”,而是靠“100個(gè)平凡的人”。全員創(chuàng )新改善是一個(gè)人辛苦前進(jìn)的100步,變成每個(gè)人前進(jìn)的 1步。 這家機械制造企業(yè)降本增效之創(chuàng )新改善的成功之處就在于夯實(shí)小創(chuàng )新小改善的基礎上發(fā)展到全系統創(chuàng )新改善。 為什么是優(yōu)先降小成本 大企業(yè)優(yōu)先降小成本,這里的小成本即小浪費、小損耗;通過(guò)持續推動(dòng)小創(chuàng )新小改善來(lái)消除這些小浪費、小損耗。 曾經(jīng)有管理咨詢(xún)界的朋友對我說(shuō),降本增效要從“痛點(diǎn)”出發(fā),如新產(chǎn)品的試產(chǎn)與量產(chǎn)是痛點(diǎn),如新產(chǎn)品的低銷(xiāo)量低毛利是痛點(diǎn),如老產(chǎn)品的品類(lèi)優(yōu)化料號優(yōu)化是痛點(diǎn),如老產(chǎn)品的高成本高損耗是痛點(diǎn),我們就從這些“痛點(diǎn)”開(kāi)始做革新做改善。 但是,我們應該明白,冰凍三尺非一日之寒,滴水石穿非一日之功,這些“痛點(diǎn)”往往是大課題,需要跨部門(mén)系統協(xié)同才能解決,如果企業(yè)內本位、官僚、部門(mén)墻嚴重,這樣的“大課題”在短時(shí)間內無(wú)法取得成效就容易流產(chǎn)。 當然,如果企業(yè)內擁有良好的領(lǐng)導力、專(zhuān)業(yè)力、協(xié)作力、執行力,優(yōu)先通過(guò)端到端系統協(xié)同解決這些“痛點(diǎn)”就必然會(huì )最快的速度創(chuàng )造最大的效益。 大企業(yè)優(yōu)先降小成本,是因為不少大企業(yè)部門(mén)墻嚴重,先通過(guò)小創(chuàng )新小改善讓員工參與降本增效,在取得一定成績(jì)后再向大創(chuàng )新大改善突破提升,這大概是這家機械制造企業(yè)降本增效之創(chuàng )新改善最值得我們借鑒的地方。
作者簡(jiǎn)介: 姜上泉,近20年來(lái)成功為100多家全球企業(yè)500強、中國企業(yè)500強進(jìn)行培訓和輔導,曾受邀為北京大學(xué)、清華大學(xué)、中山大學(xué)、上海交通大學(xué)等多所著(zhù)名大學(xué)授課。 其擁有自主知識產(chǎn)權的培訓、咨詢(xún)產(chǎn)品貫通企業(yè)經(jīng)營(yíng)管理的3個(gè)階層,高層通過(guò)《利潤空間—降本增效系統》學(xué)經(jīng)營(yíng)、做操盤(pán);中層通過(guò)《業(yè)績(jì)突破—精益管理系統》學(xué)管理、做改善;基層通過(guò)《夯實(shí)基礎—卓越班組系統》學(xué)執行、做標桿。 說(shuō)明:姜上泉導師原創(chuàng )文章,引用與轉載請注明出處和作者。 |